会员登录
MEMBER LOGIN
技术论坛
TECHNOLOGY FORUM
轨道机车车辆铸造技术的创新与展望
发布时间:
2016-09-23 00:00
来源:
摘要:本文结合戚墅堰所及部分轨道交通铸造单位多年生产轨道机车车辆关键铸件的经验,紧密跟踪目前铸造行业最新技术的发展趋势,简述了轨道交通机车车辆铸造技术的创新与应用,并对未来的发展方向进行了阐述和展望。
关键字:轨道交通 铸造技术 创新 展望
在中国经济步入新常态的大背景下,铸件整体需求增速趋稳。但近年来,随着国家对铁路行业投资的不断加大及“四纵四横”、“一带一路”战略的实施,轨道交通行业正迎来快速发展的机遇期。铸造作为机械工业的基础,对轨道交通行业的发展至关重要。根据2015年最新统计,轨道交通行业铸件占铸件总量5.2%,并且年需求增长9%,这正是对轨道交通行业快速发展的体现。轨道交通领域铸件有其自身特点,技术要求高,以中、小件为主,多数非大批量生产,同时铸造材质及铸造方式多种多样。由于轨道交通近年来高速、重载发展的需要,产品的技术要求越来越高,其中的关键铸件质量直接关系到行车安全,因此铸造技术的创新及应用是铸件品质持续提升的关键。南车戚墅堰机车车辆工艺研究所有限公司作为国内轨道交通关键零部件供应商自成立起,即以材料工艺研究为基础,以产品为导向,不断研究并应用新材料、新工艺,开发并生产了诸多轨道交通关键铸件和新材料。铸钢方面,早在80年代初期,便开始着手研究铸钢材料及产品开发,成功开发B、B+、C、D、E级钢等系列钢种,并广泛应用于摇枕、侧架、车钩、钩尾框、夹钳等零件,为铁路提速和行车安全做出了重要贡献;铸铁方面,240单体铸造活塞环获得1978年的全国科学大会奖,80年代初研制出高磷铸铁闸瓦,后续又开发出蠕墨铸铁制动盘、低温球铁活塞、电机端盖、齿轮箱等高端装备铸件,目前,已掌握各种球墨铸铁的生产技术,创造了巨大的社会和经济效益;铸铝方面,自1996年开始进行高强度铸造Al-Si合金材料制备工艺研究,并广泛应用于各型号齿轮箱的生产,先后研制了“蓝箭”高速动力车齿轮箱体、HXD1C机车齿轮箱、乌车齿轮箱、哈车齿轮箱、上海地铁齿轮箱、HXD1D机车齿轮箱、CRH380A/B动车齿轮箱、CRH6动车齿轮箱,产品种类已完全覆盖高铁、动车、城轨、机车整个轨道交通领域,使我公司生产的齿轮传动系统在中国高铁、动车、城轨市场占有率达30%以上,为中国轨道交通行业铸造技术的创新与发展做出了应有的贡献。
1 轨道交通机车车辆用关键铸钢件技术
铸钢件在轨道交通机车车辆关键零部件中占很大一部分比例,尤其是货运列车占了50%以上的比例。因此,机车车辆铸钢件质量的好坏,直接影响我国铁路运输的安全可靠性,并且也制约了我国轨道交通发展的速度?;党盗局旨捎眯录际?、新工艺,提高铸件质量,必将对我国铁路运输事业快速发展积极的推动作用。
1.1铸造合金钢精炼技术
轨道交通关键铸钢件,采用的牌号主要为符合美国AAR M201标准的A~E级钢或国标的碳素钢,主要为低合金高强度铸钢。铁路高速重载机车车辆的关键、核心部件大多为铸钢产品(如车钩、制动盘、摇枕、侧架等)。随着铁路高速重载技术的深入发展,对铁路铸钢产品的质量、性能提出了更高的要求。如对钢中氧[O]含量和夹杂物进行了严格规定。铁路关键铸钢件冶金质量的好坏,钢水中有害夹杂物不但影响钢的断裂韧性,还对钢的低、中、高周疲劳性能均产生重大影响[1]。
当前以美国、德国、日本为代表的发达国家,其铸钢的冶炼几乎全部采用炉外精炼技术。国内也有一些大型专业铸钢企业采用该技术,但大多是用于不锈钢铸件或有特殊要求的合金结构钢铸件的生产[2-3]。通过精炼技术提高铸钢件质量是铁路铸钢件生产发展的必然趋势,偏心底出钢电弧炉的留钢留渣操作,可实现无渣出钢,钢流短且呈直线状,为精炼炉提供优质钢液。LF炉、VOD/VD炉精炼具有精确控制钢水成分和浇注温度,采用喂丝吹氩工艺,降低钢中[O]、[N]、[P]、[S]含量,降低钢中夹杂物含量和改变夹杂物形态等。钢水冶炼工序主要工艺流程为:EBT电弧炉初炼(降碳、去磷、去气)——出钢(控渣、初调成分)——LF炉、VOD/VD炉精炼(升温、造渣脱硫、成分微调)——喂线(软吹)——热装塞杆——引流浇注[4]。
钢水化学成分在出钢时粗合金化过程中达到钢种规格下限,在精炼炉中微调到中限,补加合金的准确称量和氩气的充分搅拌,逐步将成分调到理想数值。脱氧、脱硫、合金化完成后,喂丝吹氩并调整铝含量,铝含量可控制在较小范围内。某种铸钢件化学成分标准见表1,随机抽取的铸钢件化学成分如表2,随机抽取的铸钢件[O]、[N]及夹杂物如表3。
1.2整体芯技术[5]
摇枕、侧架是铁路货车转向架的关键零部件,摇枕、侧架采用整体砂芯工艺,实现内腔关键部位平顺无披缝、台阶、裂纹,提高壁厚和尺寸精度,减少砂眼、芯撑等缺陷。摇枕、侧架整体砂芯,如图1所示
消除了分体砂芯带来的内腔裂纹、台阶、芯撑熔合不良、壁厚不均等质量缺陷和安全隐患。整体芯B+级钢摇枕、侧架内腔质量,如图2所示。提高了铸件尺寸精度,有利于提高转向架的运行性能和安全可靠性。批量生产的摇枕、侧架,如图3 所示。进一步优化了铸造工艺,提高了内部密实度。采用机器手下芯减少了人为因素的影响,大大提高了产品质量的稳定性,并改善了劳动条件。
整体芯B+级钢摇枕在组合载荷试验条件下,完成规定循环次数后,再加大载荷20%继续试验,所有整体芯B+级钢全部通过了120万次试验;按上述试验方法,试生产的转K6摇枕极限循环次数达184万次,转K5摇枕累计达200万次无裂纹;比原工艺和原材质提高60~80万次,并远远高于AAR等标准;整体芯B+级钢侧架完成规定循环次数后,加大试验载荷40%继续试验,累计达到50万次均无裂纹。
当前,我国摇枕、侧架的制造技术正在朝着高质量、高效益、低消耗、低污染的良性循环方向快速发展,以整体芯B+级钢摇枕、侧架制造技术为标志的我国摇枕、侧架整体制造技术和产品质量水平,已达到世界领先水平。
2 轨道交通铸造铝合金成型技术
铝合金由于密度小、比强度高、耐蚀性好,在现代交通运输业、航空航天和机电等工业领域得到了广泛应用。目前,日本、法国和德国已先后在高速列车上采用了铸造高强度铝合金齿轮箱体,轨道交通领域铸造铝合金材料工艺研究方兴未艾。
2.1 铸造Al-Si合金材料工艺研究
目前国内外轨道交通齿轮箱广泛使用的材质为ZL101A(对应EN1706中AlSi7Mg0.3),
戚墅堰所对此合金进行了系统的基础研究。除了室温条件下的拉伸性能实验外,还测定了不同环境温度下AlSi7Mg合金的力学性能。随着温度的提高,AlSi7Mg材料的抗拉强度,屈服强度具有不断降低的趋势。在-40℃~100℃范围内拉伸变形,随着温度的不断提高,合金的屈服点和抗拉强度缓慢降低,然而塑性显著提高。AlSi7Mg材料的疲劳性能对齿轮箱的疲劳寿命与可靠性也具有较大的参考价值。通过对AlSi7Mg合金的拉压与旋压疲劳性能进行了研究,结果表明在轴向加载条件下,应力比R=-1,未失效试样终止试验的循环数=105次。根据升降法测得疲劳极限为159.2MPa。在旋转弯曲加载条件下,Kt=1,未失效试样终止试验的循环数N=107次,测得合金的旋转弯曲疲劳极限≥88MPa。我们还对AlSi7Mg材料的成型特性参数进行了研究,主要是与铸造工艺性密切相关的流动性、热裂倾向和收缩率,为铸造工艺的设计提供了依据。
铝合金熔炼方面,采用国内某大型铝厂提供的ZL101A锭进行熔炼,通过AlSr10变质剂加入含量不同对比变质效果,研究表明Sr加入量在0.03-0.05%有良好的变质效果。通过加入AlTi5B,进行晶粒细化以提高材料力学性能。由于AlSi7Mg溶液有严重的吸气倾向,利用高纯氩气并采取旋转喷吹对铝液进行精炼除气,对熔炼后的铝液进行含气量测量,保证铝液纯净。
2.2铝合金低压铸造技术
目前日本、德国应用的高铁铝合金齿轮箱多采用重力砂型铸造,但对国内铝合金铸造来说,低压及压铸发展迅速,戚墅堰所一直采用低压砂型铸造。与重力铸造相比,低压铸造充型平稳飞溅少、凝固补缩效率高。经过多年探索,相继成功开发出CRH6、HXD1D、HXD1C、哈车、CRH380A、CRH380B等型号齿轮箱,产品种类已完全覆盖高铁、动车、城轨、机车整个轨道交通领域,有力的支撑公司齿轮传动系统板块的快速发展,使我公司生产的齿轮传动系统在中国高铁、动车、城轨市场上的占有份额达30%以上。目前,为进一步提高高铁动车齿轮箱的的形位尺寸精度和内、外表面质量,正在进行齿轮箱低压金属型铸造技术研究,已成功试制出CRH380A箱体样件。
3.轨道交通铸铁件关键技术
轨道交通铸铁件主要有活塞及活塞环、柴油机机体、制动盘、齿轮箱、抱轴箱、制动零件等等,当前相关材料工艺研究主要集中在以下方面:
3.1超低温高韧性球墨铸铁件的生产技术
为适应部分寒冷地区的恶劣自然条件,普通的球墨铸铁件已难以满足设计需求。某些铸件,例如转向架轴箱、齿轮箱等都普遍要求-40℃甚至-60℃的冲击值达到12J。目前,国内仅少数生产单位能够稳定生产出-40℃的低温球铁件,其主要途径为,采用优质高纯生铁等原材料、辅以特定的熔炼工艺等来获得高品质的原铁水,并严格限制有害元素含量,强化过程控制。
3.2高端铸铁件的生产技术
轨道交通铸铁件对于产品的内、外部质量要求较高,普遍的标准是DIN1690-S2-RV2,即磁粉探伤满足EN 1369中规定的2级,射线探伤满足ASTM规定的2级,这对铁水的熔炼质量以及工艺设计提出了较高要求,盖包球化、喂丝球化等环境友好型球化处理技术是国外发达工业国家常见的球化处理方法,但国内应用较少,可进行研究推广;多次孕育处理、随流孕育,铁水预处理等技术,是获得高端铸铁件不可或缺的手段,将会得到更多、更好的应用;与此同时,各类球化剂、孕育剂等铸辅材料的应用也将更加专业化。同时,铸件外观质量、尺寸精度要求也不断攀升,比普通铸件要高1-2级,模具制作、造型、制芯、涂料、清理、打磨等工序需要更加严格控制,采用自动化静压线造型、各类冷、热芯盒制芯,流涂、浸涂,自动打磨机等新装备、新技术得到越来越多的应用。
4.铸造模拟仿真技术
轨道交通关键零部件如连接系统车钩、缓冲器、传动系统齿轮箱、制动系统夹钳、大型关键零部件柴油机机体、转向架摇枕和侧架等大多使用铸造方式进行生产,其质量好坏直接关系到机车的安全性。为生产高质量、高精度的铸件,目前工艺设计人员普遍先采用铸造模拟仿真技术预测铸件可能产生的铸造缺陷,再在模拟仿真结果基础上进行工艺优化和试验验证,缩短开发周期并快速获得合格铸件。
戚墅堰所等企业主要采用MAGMAsoft软件进行模拟仿真,涉及的铸造方式主要包括砂型铸造、低压铸造、熔模铸造、离心铸造和金属型铸造等,铸造过程数值模拟流程如图4所示。
图4铸造过程数值模拟流程
摇枕和侧架均属于大型铸件,型号众多,年消耗量大,南车集团公司内部有南方汇通公司、长江公司及戚墅堰公司等生产各种不同型号的摇枕和侧架。在某机型车的摇枕和侧架开发过程中,戚墅堰所分别采用了ProCAST软件和MAGMAsoft软件进行模拟分析和对比。图5和图6分别为基于ProCAST软件和MAGMAsoft软件对侧架铸件易出现缩孔缩松缺陷部位的模拟结果,从图5和图6中对比分析可知,三个易出现缩孔缩松缺陷的部位中,两软件预测的缩孔缩松缺陷的大小和位置基本相同。经对出现缺陷部位进行工艺改进后,缺陷得到了消除,缩短了开发周期,为实际生产提供了可靠性依据,满足了客户的交货时间要求。
动车组车钩属箱形结构,铸件壁薄,主要壁厚只有12mm,厚大部位超过40mm,壁厚相差悬殊,而且内部有多个空腔,容易产生缩孔缩松和浇不足现象。如图7所示的原设计工艺中解钩杆上部筋交际处、后腰部位和钩舌腔有明显的缩孔缩松缺陷。通过模拟仿真进行工艺改进后,缺陷基本得到消除,如图8所示,且由原来的一模一件改为一模两件后工艺出品率提高了10%以上,成品率超过96%。同时原方案生产的中间钩铸件进行拉吨试验时,在拉力为110吨时发生断裂,对工艺优化后生产的铸件进行拉力试验的吨位达到171吨,优质的铸件质量确保了该产品使用可靠性以及行车安全。
制动夹钳铸件结构复杂,壁厚相差很大,最薄处为10mm,最厚处为66.5mm,铸造难度大。图9所示的原工艺方案中在圆环区域两侧的区域存在大面积的缩孔、缩松,经对工艺改进后,圆环形区域两侧出现缩孔的缺陷较之以前有所减少,如图10所示。将优化后的铸造工艺方案应用于实际生产中,能够提高铸件的成品率,提高了近10%,确保了产品使用可靠性以及行车安全。
铸造模拟仿真技术在轨道交通关键零部件中的应用较广泛,取得了较好的效果,尤其在关键零部件中的国产化、铸造质量改进和缩短开发周期等方面起到了较好的作用,确保了产品使用可靠性以及行车安全,对满足和促进铁路高速重载的发展有重大的意义。此外,国外引进关键零部件铸件价格昂贵,国产化后生产成本低廉,可节约成本近80%,创造了大量的经济效益和社会效益。
5.发展趋势展望
5.1 3D打印技术
3D打印技术近年来发展迅速,并得到越来越广泛的应用,其在新产品开发、复杂结构制造、传统工艺难以加工以及个性化定制等方面具有传统工艺不具备的优势,具有较强的市场应用前景,目前该项技术在航空航天,医疗、汽车、文化创意、设计等领域得到了较大程度的应用。3D打印技术根据所用的设备、成形材料及成形制件等特点基本可以归结为6种基本方法,即熔融沉积制造(FDM)、光固化(SLA)、实体叠层制造(LOM)、选择性激光烧结(SLS)、三维喷涂粘接(3DP)、金属直接增材制造等。
3D打印技术为传统铸造行业提供了快速制造铸型、型芯的技术手段,给铸造行业带来了新的发展机遇。3D打印技术与传统铸造技术的结合,能够迅速的实现从设计到产品的过程,减少中间环节,加快产品开发周期,降低成本,尤其适合单件新产品试制或者小批量结构复杂铸件的生产,如结合选择性激光烧结成型SLS技术的快速砂型铸造已经成为目前发动机样件试制的最常用和最有效的方法。目前利用SLS技术快速制造铸件的工艺路线主要有两种:一种是直接烧结覆膜砂或者陶瓷粉,制造砂型或者砂芯用于重力或低压铸造;另一种是烧结高分子塑料或者石蜡材料,通过熔模铸造的方法快速制造金属零件。随着3D打印设备及耗材的技术进步,必将对铸造模具制造、复杂砂型和砂芯、蜡模、消失模等成型带来深刻的变革。
5.2 智能技术
近年来,随着产业升级及劳动力成本的上升,智能机器人及自动化设备正迅速应用于各行各业。在铸造领域,目前自动化的造型、浇注生产线早已屡见不鲜,机器手臂在下芯、合箱、浇注、切割浇冒口及去毛刺等各工序也已得到广泛应用,自动化技术使得传统铸造正在向绿色铸造、智能铸造加速转变。此外,铸造模拟仿真技术在缺陷的预测方面也更加全面、可靠,并从传统的分析缩松缺陷,扩大到分析夹渣、裂纹、冷隔等外部缺陷方面,甚至能预测金相组织及力学性能,最终对产品的使用性能做出评价。相信在不久的将来,铸造将真正由经验型向智慧型转变,铸件质量也可以得到稳定的有效控制。
5.3 铸钢、铸铁新材料研究及应用
由于产品使用要求的不断提高,铸钢、铸铁新材料开发及应用需求更加广泛。结合具体
产品,针对目前货用车钩钩体及钩舌裂损惯性质量问题,需重点开发高强韧铸钢材料及制造工艺研究;针对工程机械耐磨铸钢件如耙板、捣镐等耐磨件耐磨性偏低的特点,亟需开展新型高耐磨高韧性铸钢材料技术攻关,开发新型高耐磨铸钢材料,提高磨耗产品的耐磨性及服役寿命;针对动车组铸钢制动盘及其它关键铸钢零部件对铸件本体夹杂物及气体含量要求较低的现状,开展中频炉钢水净化技术及高纯净钢材料制备工艺研究,降低钢水中的气体及夹杂物含量,提高钢水品质,保证产品内在质量和性能。
新型铸铁材料及工艺开发方面,开展新型铸铁材料及制造工艺的开发,发展新型高性能球墨铸铁材料,拓宽其应用范围;开发新型耐低温高性能球铁材料及制造工艺,提高耐低温球铁件的服役性能,拓宽其应用领域;合金化是提高铸铁性能的重要手段,通过合理调整Si,Mn,Cu,Ni,Mo等合金元素的成分,可以生产出综合力学性能优异的各类铸铁件,例如生产出高强度高塑性的QT550-10、QT600-7材料,也可以显著提高铸铁件的使用寿命,如提高蠕铁制动盘的耐磨性和韧性;研究各种合金化铸铁的力学性能及使用性能,既扩大了铸铁材料的应用范围,也为代替各种轨道交通铸钢件提供了基础支撑。
5.4铝合金材料工艺发展趋势
5.4.1 Al-Cu系合金
铸造铝合金除Al-Si系外,还有Al-Mg、Al-Zn和Al-Cu系铸造合金,Al-Mg系铸造铝合金室温强度虽高,但高温性能较差,铸造工艺性也不如Al-Si系合金。Al-Cu合金是典型的高强韧铸造铝合金,合金强度高,塑性、韧性较好,同时兼具较高的热稳定性,适于高温下使用的铸件,但铸造性能普遍较差,易发生热裂。目前已工业化应用的高强韧铝合金(Rm≥400MPa,A≥8%)几乎全是Al-Cu系合金。国内研制的ZL205A(AiCu4Ti)合金,抗拉强度可达510MPa,延伸率可达13%,是目前强度最高的铸造铝合金。ZL205A合金可以实现以铝代钢,以铸代锻,制作高难度的优质铸件。
随着轨道交通装备朝着高速、节能、安全、舒适的方向发展,对铸造铝合金产品的性能和质量提出了更高的要求,在轻量化的同时越来越追求合金的高强度和延伸率。然而由于铸造工艺性能较差,高强韧铸造Al-Cu系合金在轨道交通领域的应用还几乎是空白,未来需要在提高Al-Cu系合金材料的铸造性能和新的铸造工艺技术两方面取得突破。
5.4.2 铝基复合材料
早在60年代初期,即开始了对铝基复合材料的研究。初期研究主要是针对铝合金基体和增强颗粒、增强纤维的复合,研究复合材料各方面的性能。复合材料的性能较原基体铝合金在强度、刚性、耐热、耐腐性等方面均有大幅度的提高。铝基复合材料具有高的比强度、比刚度和优良的高温力学性能以及低的膨胀系数和优良的耐磨性,在轨道交通、航空、航天、汽车等工业领域具有十分广泛的应用前景,是当前金属基复合材料研究的热点,也是铸造铝合金发展的新方向。用铝合金复合材料制作的轨道交通用的刹车制动盘,可减重50%~60%,减小了惯性力,增大了制动加速度,提高了导热速度,减小了磨损,从而改善了制动盘的性能。目前戚墅堰所正在开展轨道交通用铝基复合材料制动盘的研究。
5.4.3 真空差压铸造
真空差压铸造是一种在低压铸造方法上改进的先进铸造方法,使金属液在可调压力下充型及凝固,故具有一系列有利于获得优质铸件的因素:能消除铸件气孔、缩孔、缩松等缺陷;改善铸件表面的粗糙度;明显减少大型复杂铸件凝固时的热裂倾向;补缩能力是低压铸造的4~5 倍;而且可减少凝固时间20%~25%,相应地也减少了凝固期内的变质衰退现象,而且其晶粒也有所细化。真空差压铸造目前其工程化应用对象还局限于航空类铝合金铸件,但随着这项技术的进一步成熟,成本进一步降低,其应用领域扩展到轨道交通铝合金齿轮箱体成型方面将势在必行。
6结束语
在新技术、新装备、新材料、新工艺的不断发展和升级下,铸造正快速得由传统的高能耗工业,向绿色铸造、智能铸造转变。轨道交通的快速发展推动了相关技术在本领域的创新和应用,取得了较好的效果,产品使用可靠性以及行车安全系数不断提高,对满足和促进铁路高速重载的发展有重大的意义,同时也创造了大量的经济效益和社会效益。
附件下载:

-
地址:济南市解放路134号 电话:0531-86401781 / 86952422 传真:0531-86465075
邮箱:foundry-shandong@163.com 邮编:250013
版权所有 © 山东省铸造协会 鲁ICP备2021002429号
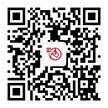
官方公众号